Heat Sink
- tecqusition
- Dec 29, 2021
- 4 min read
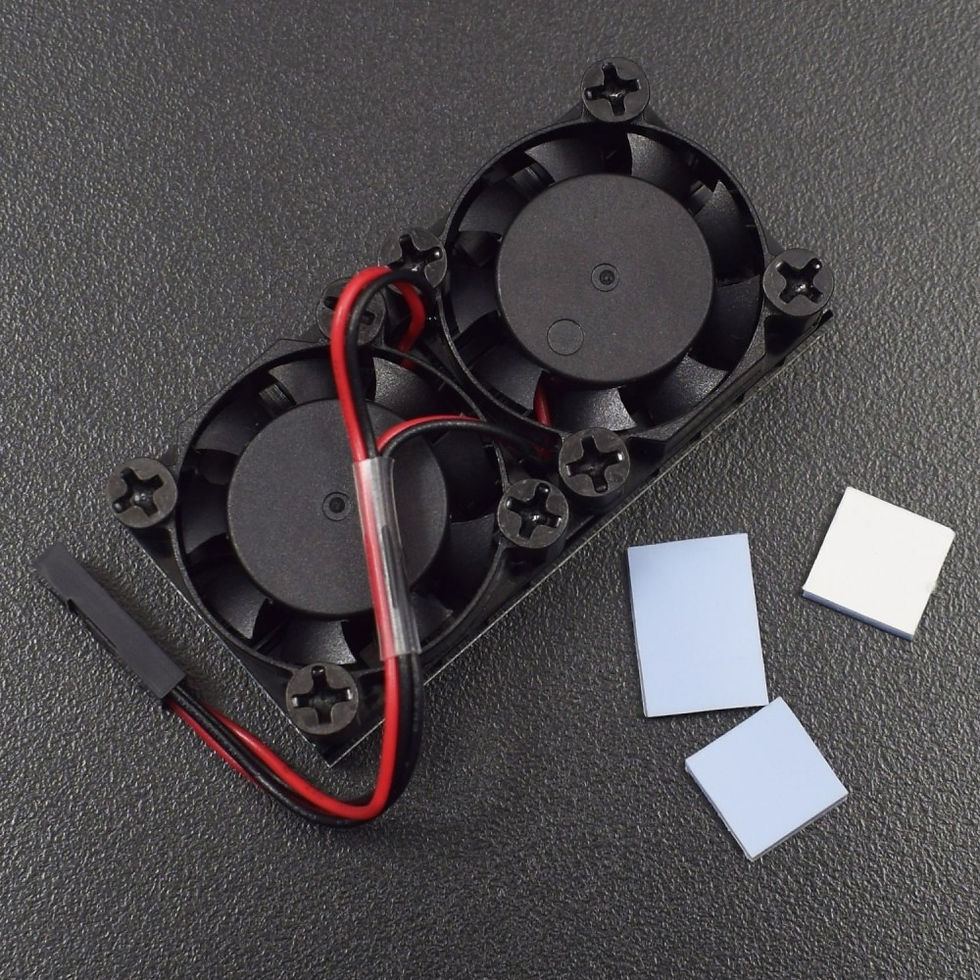
What is a Heat Sink? A heat sink is a component that increases the heat flow away from a hot device. It accomplishes this task by increasing the device's working surface area and the amount of low-temperature fluid that moves across its enlarged surface area. Based on each device's configuration, we find a multitude of heat sink aesthetics, design, and ultimate capabilities. You can see a straight fin heat sink in the image at the top of this article and a flared fin heat sink in the image below. Each heat sink is valuable in applications that may have varying:
How Does a Heat Sink Work? A heat sink works by moving heat away from a critical component. Nearly all heat sinks accomplish this task in four basic steps:
The source generates heat. This source may be any system that creates heat and requires the removal of said heat to function correctly, such as: - Mechanical - Electrical - Chemical - Nuclear - Solar - Friction
Heat transfers away from the source. Heat pipes can also aid in this process, but we'll cover those components separately. Indirect heat sink-contact applications, heat moves into the heat sink and away from the source via natural conduction. The heat sink material's thermal conductivity directly impacts this process. That's why high thermal conductivity materials such as copper and aluminium are most common in the construction of heat sinks.
Heat distributes throughout the heat sink. Heat will naturally travel through the heat sink via natural conduction moving across the thermal gradient from a high temperature to a low-temperature environment. This ultimately means that the heat sink's thermal profile will not be consistent. As such, heat sinks will often be hotter towards the source and cooler towards the sink's extremities.
Heat moves away from the heat sink. This process relies on the heat sink's temperature gradient and its working fluid―most commonly air or a non-electrically-conductive liquid. The working fluid passes across the surface of the warm heat sink and utilizes thermal diffusion and convection to remove heat away from the surface and into the ambient environment. This stage relies on, yet again, a temperature gradient to remove heat from the heat sink. Therefore, if the ambient temperature is not cooler than the heat sink, no convection and subsequent heat removal will occur. This step is also where the total surface area of the heat sink becomes most advantageous. A large surface area provides an increased area for thermal diffusion and convection to occur.

Active Heat Sinks vs. Passive Heat Sinks Heat sinks are most commonly utilized inactive, passive or hybrid configurations.
- Passive heat sinks rely on natural convection, meaning the buoyancy of hot air alone causes the airflow generated across the heat sink system. These systems are advantageous as they do not require secondary power or control systems to remove heat from the system. However, passive heat sinks are less effective at transferring heat from a system than active heat sinks.
- Active heat sinks utilize forced air to increase fluid flow across the hot area. Forced air is most commonly generated by a fan, blower, or even movement of the entire object―such as a motorcycle's engine being cooled by the air passing along the heat sink fins designed into the engine. One example of a fan producing forced air across a heat sink is the fan in your personal computer turning on after your computer gets warm. The fan forces air across the heat sink, which allows more unheated air to move across the heat sink surface, thus increasing the total thermal gradient across the heat sink system and allowing more heat to exit the overall system.
- Hybrid heat sinks combine some aspects of passive and active heat sinks. These configurations are less common, and they often rely on control systems to cool the system based on temperature requirements. When the system operates at cooler levels, the forced air source is inactive, only cooling the system passively. Once the source reaches higher temperatures, the active cooling mechanism engages to increase the cooling capacity of the heat sink system.

Popular Heat Sinks As we mentioned, heat sinks are most commonly found in CPUs in computers. For example, the Jetson Nano has a large heat sink to assist in cooling the onboard Quad-core ARM A57 CPU and 128-core NVIDIA Maxwell GPU, both of which create ample amounts of heat and require exceptional cooling to avoid thermal throttling. Similarly, Raspberry Pi microcontrollers have a built-in heat dissipator, which they use in conjunction with a heat sink to increase the onboard Broadcom chip's performance. You can find stock heat sinks to cool the most common chip sizes. Some heat sinks are custom designed to handle a specific chip or device's thermal loads best.
FOLLOW US ON INSTAGRAM, FACEBOOK AND PINTEREST
DISCLAIMER
The information is provided by Tecquisition for general informational and educational purposes only and is not a substitute for professional legal advice. If you have any feedback, comments, requests for technical support or other inquiries, please mail us by tecqusition@gmail.com.
Comments